A brushless motor encoder is a device used to monitor the position, speed, and direction of rotation of the rotor in a brushless DC (BLDC) motor. It provides critical feedback to the motor controller, enabling precise control over the motor’s performance. Unlike brushed motors, which rely on brushes and a commentator to track rotor position, brushless motors require an encoder because they have no brushes to provide position information.
How Brushless Motor Encoder Work
The basic function of an encoder in a brushless motor is to detect the rotor’s position. This is typically achieved through optical or magnetic sensing methods:
Optical Encoders: Brushless Motor encoder uses a light source and a photo detector to read patterns on a rotating disc attached to the rotor. As the rotor turns, the disc interrupts the light, creating pulses that the controller can count.
Magnetic Encoders: Instead of using light, magnetic encoders rely on a rotating magnetic field to detect position. They are more durable than optical encoders and perform better in harsh environments.
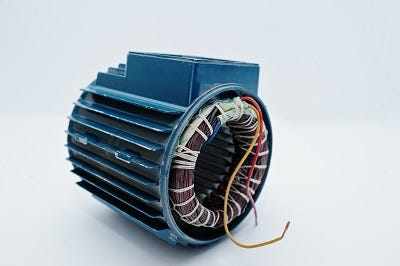
Agv Drive UnitWhy Are Brushless Motor Encoder Essential?
Precise Motion Control
Brushless motor encoder delivers real-time information about the rotor’s position, speed, and direction, enabling the motor controller to adjust the motor’s performance dynamically. This level of precision is necessary for applications that require smooth and accurate motion, such as robotics, CNC machines, and electric vehicles. Without this feedback, controlling the motor precisely would be challenging, leading to instability and inaccurate movements.
Efficiency in Operation
Brushless motor encoder is often used in applications that require variable speeds and loads. The encoder provides feedback on the motor’s rotational speed, allowing the motor controller to adjust power input accordingly. This optimization helps improve energy efficiency by reducing wasted power and heat generation, making the motor more efficient and extending its lifespan.
Enabling Closed-Loop Control Systems
A closed-loop control system uses encoder feedback to make continuous adjustments to the motor’s operation. This constant feedback loop ensures that the motor operates within the desired parameters, automatically correcting any deviation in speed or position. These results in smoother motion, better performance, and higher reliability, as the system can react to changes in real-time (e.g., load variations, motor speed changes, or resistance).
Prevention of Motor Stalls
Encoders help prevent motor stalls by providing real-time information on motor speed and position. If the motor begins to slow down or faces excessive load, the encoder signals the controller to adjust the power input. This feedback prevents the motor from stalling, protecting the system from potential damage, performance loss, or failure.
Improved Torque and Speed Control
With precise data from the encoder, the motor controller can finely control the motor’s torque and speed. In applications such as electric vehicles, drones, and industrial machinery, controlling both torque and speed accurately is vital for smooth operation and overall system performance.
Key Considerations When Choosing a Brushless Motor Encoder
Resolution
The resolution of the encoder determines how finely the rotor position can be measured. A higher resolution provides more precise control, which is essential for applications that require high accuracy.
Cost vs. Performance
While absolute encoders provide superior performance, they are more expensive than incremental encoders. When choosing an encoder, it’s important to balance the cost against the performance requirements of your application.
Size and Compatibility
Ensure that the encoder is compatible with the brushless motor in terms of size, mounting options, and communication protocols.
Conclusion
Brushless motor encoder is essential components for ensuring precise control and efficiency in systems that use brushless motors. By providing real-time position, speed, and direction feedback, encoders enable smoother operation, prevent motor stalls, and extend motor lifespan. Whether in robotics, electric vehicles, or industrial automation, the integration of an encoder with a brushless motor transforms it from a basic power source into a highly efficient, precision-driven system.
Write a comment ...